20 consejos para diseñar un sistema de aire comprimido
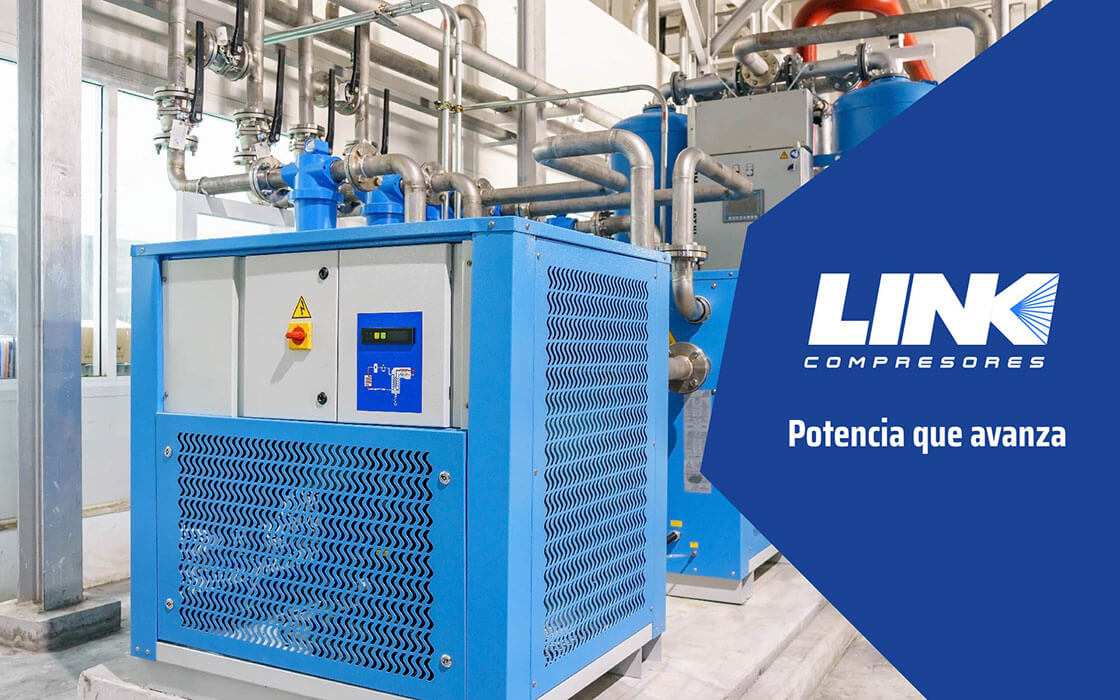
Un sistema de aire comprimido está compuesto por una serie de elementos, que a su vez poseen sus funciones esenciales. Se dividen en dos:
Elementos de compresión y elementos de distribución.
Cuando hablamos de elementos de compresión nos referimos a los siguientes dispositivos: compresor y tanque. Dichos elementos se denominan “fijos”, puesto que siempre estarán en la base de todo sistema de aire comprimido.
Por otro lado, también se encuentran el secador y el filtro o filtros, que serían los elementos variables, puesto que podrían ser uno o más. Además existen los elementos de compresión, que son aquellos que producen el aire comprimido,
Y, por último, los elementos de distribución, cuando hablamos de ellos nos referimos a la red de aire, red neumática o red de tuberías, que son los encargados de distribuir el aire comprimido hacia las distintas herramientas neumáticas de nuestra red de aire comprimido.
Sobre estos elementos de distribución se trata este artículo.
Veamos entonces 20 consejos que hemos preparado para que los tomes en cuenta, a modo de tips, antes de instalar un sistema de aire comprimido:
1.- Determinar para qué necesitas la red de aire. Eso implica analizar todas las variables posibles y determinar así el tipo de instalación y el tipo de compresor necesario.
2.- Calcular la presión de aire comprimido. Se debe realizar a fin de establecer un óptimo funcionamiento del compresor y la red de aire comprimido. El trabajo de tipo industrial requiere una presión entre 6 y 7 bar.
3.- Calcular el caudal de aire comprimido. El caudal de la red debe ser calculado con base en el trabajo a realizar, en la cantidad de aire comprimido que se necesita y además considerando posibles trabajos futuros, esto con el propósito de no realizar mayores cambios a la red de tuberías.
4.- Estimar las pérdidas de aire por presión. Los elementos de la red de aire comprimido como válvulas, codos, equipos y otros, se oponen al flujo de aire generando pérdidas de presión. Calcular una cantidad de pérdida razonable será esencial en el diseño para evitar grandes desperdicios. Se recomienda que sea inferior al 5%.
5.- Determinar la velocidad de circulación del aire. La velocidad también debe controlarse puesto que esta produce igualmente pérdidas por presión.
6.- Garantizar el estudio de la estructura del edificio. Será necesario tomar en cuenta el espacio suficiente para posibles variaciones en la longitud de la tubería durante el proceso de instalación e incluso para futuras reestructuraciones.
7.- Asegurar que la estructura de las tuberías sea lo más recta posible. Los cruces producto de codos y demás elementos se oponen a la circulación del aire provocando pérdidas.
8.- Instalar la tubería siempre de forma aérea. Esta facilita la instalación de las herramientas en los puntos correspondientes además de facilitar el mantenimiento en caso de fugas.
9.- Dejar espacio suficiente para la estructura de tuberías puesto que al momento de circulación de aire sufren dilatación por el cambio de temperatura.
10- Colocar estratégicamente diversas llaves de paso para detener y controlar el suministro y así no interrumpir el funcionamiento de la red. En el caso de realizar un mantenimiento en un área determinada no se verá afectado todo el sistema.
11.- Instalar las tomas de aire en la parte superior. Esto con la finalidad de no recoger agua condensada u otros elementos que dañen la calidad del aire que se distribuye en las distintas herramientas neumáticas conectadas a la red.
12.- Medir constantemente la pérdida de presión. No superar un 5% de pérdida es lo recomendable.
13.- Conectar siempre antes de la toma de un equipo neumático el filtro, regulador de presión y un lubricador.
14.- Instalar el compresor a una distancia entre 7 y 10 metros de la primera herramienta para que el aire salga a una temperatura adecuada.
15.- Colocar mangueras flexibles y con entradas acordes entre el compresor y la red, con la finalidad de evitar vibraciones.
16.- Prever conexiones futuras soldando niples en áreas estratégicas.
17.- Usar materiales de buena calidad. Se sugiere evitar cañerías plásticas soldadas por fusión de plástico. Es recomendable el uso de: acero inoxidable, cobre, acero negro, acero galvanizado y aluminio.
18.- Escoger tuberías de mayor diámetro reducirá las velocidades de aire, y por lo tanto el nivel de turbulencias, con una pérdida mínima de presión.
19.- Garantizar el mantenimiento general del sistema de aire industrial, así como el de los dispositivos individuales, para evitar daños y disminución en la producción y calidad del caudal de aire comprimido.
20.- Consulte a los expertos para evitar daños, y sobre todo una mala inversión.
Como se habrán dado cuenta, el objetivo de la instalación de un sistema de aire comprimido es producir un caudal de aire ideal para sus respectivos usos, evitando la pérdida de presión, así como tener un dispositivo capaz de evitar la introducción de elementos que contaminen la calidad del aire.
Tomar en cuenta todos los elementos de su construcción e instalación, así como elegir los mejores materiales, equipos y por supuesto a los profesionales capaces de realizar esta tarea, nos garantizará cumplir nuestros objetivos de tener una red de aire industrial productiva y eficiente.