10 razones para cambiar tu compresor de pistón por un compresor de tornillo
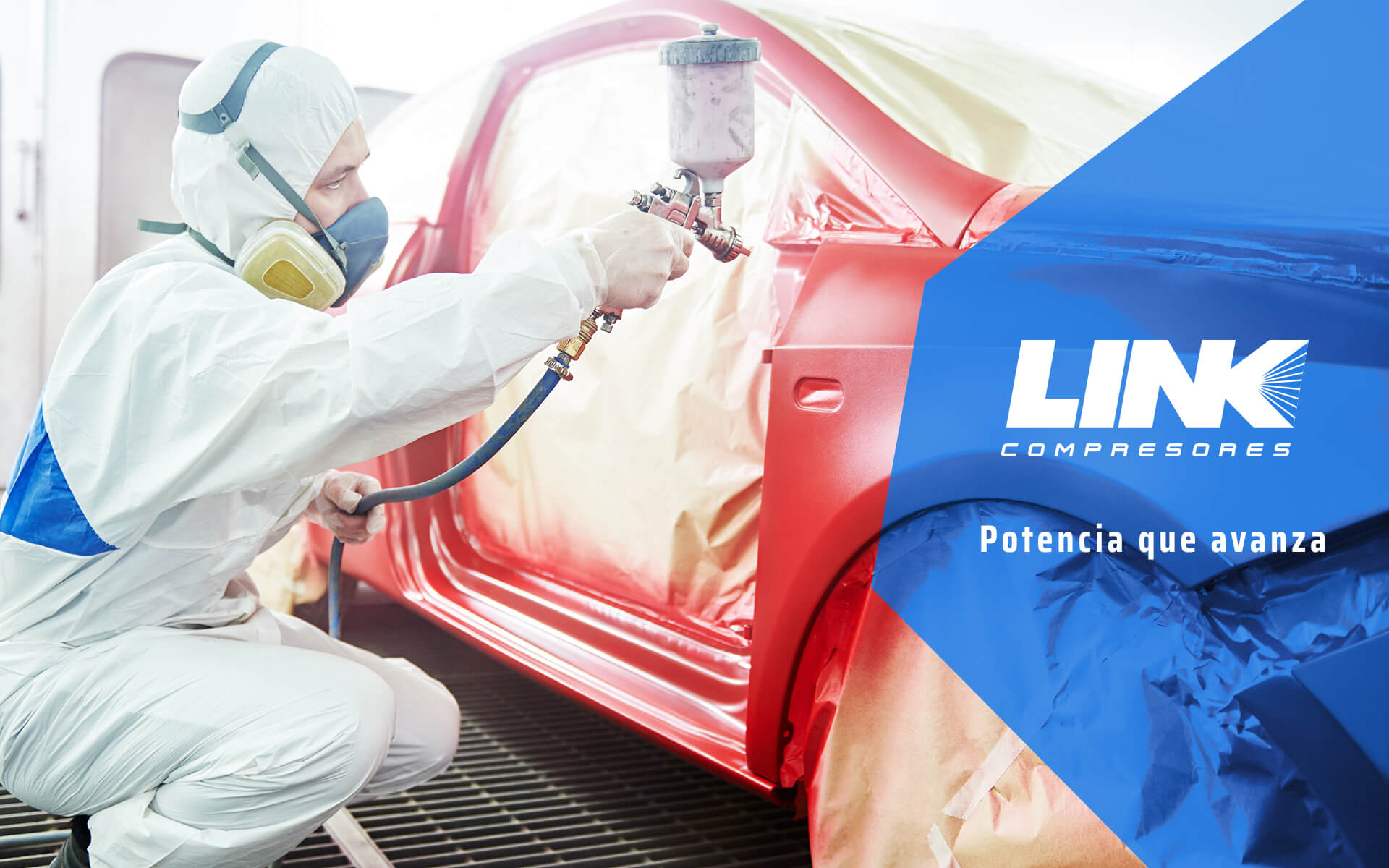
Una pieza fundamental de los compresores de pistón es el cabezote que a diferencia de los tornillos helicoidales de una unidad de aire para un compresor de tornillo no están diseñados para trabajo continuo. El cabezal, en los compresores de pistón, funciona como su nombre lo indica con el principio de funcionamiento de un pistón para comprimir el aire que ingresa a la máquina.
Como podremos darnos cuenta, el cabezal es el corazón del compresor de pistón, es un componente muy importante y requiere especial atención. En algunos casos los cabezales presentan fallas muy específicas que obligan al cambio inmediato del compresor.
Es por ello que aquí te mostramos 10 razones para evaluar si es una necesidad prioritaria el cambio de tu compresor de pistón por uno de tornillo:
1.- Presenta presión más alta de la requerida:
Aunque los compresores generan un aumento en la presión, se debe tener especial cuidado de no acostumbrarse a una sobre-presión en el sistema, ya que cada 10 psi de presiones adicionales en la configuración del compresor implican un aumento en el consumo de electricidad cercano al 4%.
También el aumento de presión puede darse por una acumulación de aceite en la línea que está obstruyendo el paso del aire generando aumento en la presión y pérdida de caudal de aire, éste problema se puede derivar de la falta de un correcto tratamiento de aire.
Si has atendido una falla similar, ya sabes que tienes una oportunidad de mejorar el tratamiento de aire o hasta cambiar a una tecnología de compresión más robusta como tornillo que asegura un paso menor de aceite a tu proceso.
2.- Calentamiento excesivo:
Los compresores de pistón NO están diseñados para trabajo continuo, están diseñados para trabajo intermitente, lo que quiere decir que están diseñados para trabajar un 60% del tiempo y descansar el otro 40%.
De no ser así y mantenerlos encendidos continuamente en un día de trabajo generará aumento en la temperatura de las partes internas desencadenando daños y paradas en el proceso, dentro de los fallos típicos se puede encontrar el desgaste de los anillos y hasta la fundición de los cabezales.
3.- El cilindro no succiona aire, no hay succión de ningún tipo:
Pueden presentarse problemas en los pistones si no están correctamente sellados en su cámara de compresión, por ejemplo puede haber fugas en las recámaras del cabezal o las válvulas pueden estar en una posición incorrecta. Puede ocurrir debido al movimiento constante o desgaste generado por operación continua.
4.- El compresor tarda mucho en apagar:
En este caso, la velocidad del compresor es mayor que la necesitada. Suele suceder por sobrecarga del motor. También genera presión muy alta de la descarga del caudal de aire.
5.- No hay movimiento a nivel de cilindro:
Puede ser provocado por una vibración que no ha sido controlada e irremediablemente ha afectado los componentes del cabezal. Dicha falla ocasiona un incorrecto funcionamiento en los cilindros, además de desbalancear el motor, afectando su correcto funcionamiento.
6.- No hay presión:
Si ya has revisado las tuberías, el tanque, y no hay ningún problema entonces hay fugas en algún componente del cabezal. Tanto a nivel de desgaste en los empaques de la cabeza del cilindro, como válvulas desgastadas.
7.- Excesiva vibración en el cabezal:
Esto sucede por el desgaste de los componentes que lo fijan, específicamente de los tornillos y de las partes en que está sujeto el cabezal. También porque las refacciones están mal instaladas o ya han pasado su vida útil.
8.- La placa interna de las válvulas están rotas:
Suele ocurrir por falta de mantenimiento. La vibración puede dañar otros componentes, es por ello que se procede a cambiar el compresor completo. Por esta razón es tan importante el mantenimiento en los tiempos correspondientes.
9.- La válvula y otros componentes internos se han quemado:
No tenemos otra alternativa y debemos cambiar las piezas o el equipo, sin embargo te recomendamos hacer un análisis de la razón por la cual esta situación se presentó, puede ser por alguna razón expuesta anteriormente o. te recomendamos en este caso revisar las fuentes de energía en donde habías conectado el compresor, puesto que podría tener una fuente de voltaje o muy alta o demasiado baja. Asegúrate que el nuevo equipo esté conectado a la fuente de poder correcta.
10.- El motor se quemó y no hay movimiento en la correa:
Nuevamente se debe a problemas de voltaje. Este caso es irremediable y debes cambiar el compresor. Es preferible cambiar el equipo entero a sustituir partes, puesto que generalmente otros componentes han sido dañados debido al voltaje. De nuevo es imperativo revisar urgentemente la fuente de poder en donde tienes conectada la máquina para evitar daños similares a futuro.
Es muy importante que sepas: no todas las fallas tienen que ver con el cabezal. También puede deberse a otros componentes internos. Claro, no esperes a que esto suceda, imponte una disciplina rigurosa en cuanto al mantenimiento preventivo del equipo.
Este tipo de fallos requieren cambiar el equipo entero, pues que de no hacerlo nos volveremos esclavos de reparaciones constantes.
Cuando el equipo presenta estos inconvenientes y nos limitamos solo al cambio de refacciones y demás componentes dichas acciones no producen mejoras, solo dolores de cabeza permanentes.
La vida útil de los compresores de aire industrial varía dependiendo del modelo y sobre todo del mantenimiento que reciban. En el caso de los compresores de pistón se estima alrededor de 4 a 6 años de vida útil.
Es por ello que siempre requieren una revisión en manos de expertos, de al menos 3 o 4 veces al año, para así garantizar su correcto funcionamiento.